Clermont Clay Products
Company
The largest industry in the history of
Clermont was the Tile Plant (as it was known by most residents). The
Commonwealth of
Pennsylvania
chartered the Clermont Sewer Pipe Company in February of 1904.
Attorney John G. Whitmore was responsible for its formation.
The officers for the new company were President, M. F. Quinn,
Vice-President, F. Barclay, and Secretary and Treasurer, W. E. Ringrose. In 1904
the construction of the new industry had begun. They built a factory and 21
company houses and new industry had begun. Each
row of houses was comprised of seven houses. Each row was named. The row on top
of the hill was called the Black Row. The other two were the King Row and the
Queen Row. The original purpose of the factory was to manufacture salt glazed
sewer pipe in various sizes. One
example is the six-inch pipe seen here.
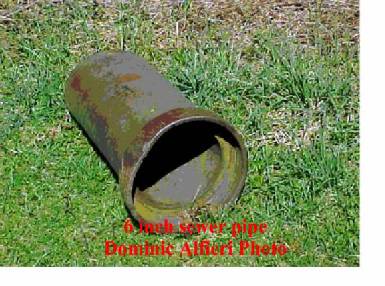
The
local residents also found various uses for some of the sewer pipe as seen in
this 30-inch pipe being used as a planter.
The manufacturing of the tile
involved four operations. First was the mine, which supplied the clay for the
tile and the soft coal, which was used to fire the boilers and also the kilns.
Some additional coal was
brought in by rail to meet the needs of the plant. Esther Aloi’s uncle,
Harry Flickinger, was the mine foreman. The
following miners worked there: Albert Anderson, Willard Rounsville, Fred Hagman,
Fred Henry, Art Jacobson, Art Marshall, Kurt Marshall, Leander(Slim) Marshall,
Blacky Henry, Dick Johnson, Dominic Cecchi.
Aaron Miller, Jim Fowler and Fred Murray. Here is a photo of some of the
miners that worked in the Clermont Clay Products Company mine in Clermont.
Front row left to right: Jack Sample, Fred Henry, Dick Johnson, Bill Burford, Bill
Henry, Kurt Marshall, Aaron Miller, and Willard Rounsville. Esther Aloi
identified the men in the front row. I have not been able to identify the men in
the second row.
On March 23, 1923 Albert Anderson and Willard Rounsville were in the
mine working together when an accident occurred. Willard was holding some
dynamite caps in his hand and Albert bent over causing his carbide lamp to touch
the caps. Consequently the caps exploded and severed Willard’s arm. Willard
recovered but was unable to work in the mine any longer so was assigned to run
the waterworks. Here is a Photo of Albert Anderson and Willard Rounsville.
Second, was the factory
complex which included the building where the tile were made, a boiler room for
producing steam, and a blacksmith’s shop for necessary repairs etc.
Third was the kiln area where originally 12 kilns were built.
Finally the yard where the tiles were stored until they were shipped.
In addition there was a siding from the
Pennsylvania
Railroad and in later years one from the Shawmut Railroad.
1.
Company houses called the Black Row
2.
Pennsylvania
Railroad Station
3.
Screening area for screening clay from dry pans
4.
Smokestack for the boilers
The factory was a four-story
building with a small room on top that housed the screens for screening the clay
after it had been ground. On the
right side of the first floor in a separate room called the engine room a steam
engine was housed. It served to
drive all the machinery in the plant itself.
To the right of the factory another building was located that contained
four boilers. They were coal-fired boilers and provided the steam to run the
engine and to provide heat throughout the plant for drying the tile. Water for
the boilers was pumped to a tank on the hill above the boiler room and above the
present day firehouse.
Just below the boiler room was
an entrance to the mine. It was used
primarily to enter and exit the mules that were used in the mine.
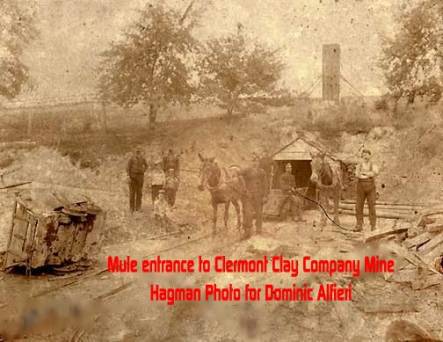
To the right of the boiler
room was a huge round smoke stack that served the boiler room.
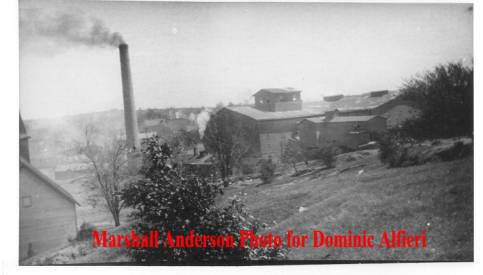
The
ashes from the boilers were wheeled out and dumped over the bank near the
entrance to the mine. During the 1930’s and 1940’s ashes were used on hills
on the highways and in the local towns. They were used especially the hill from
Hazlehurst to
Mt.
Jewett
on Route 6. So many of these ashes
came from this plant in Clermont.
In the early 1935 the smokestack was struck by lightning and
severely damaged. It was decided
that it should be brought down and a new one built. It was leaning dangerously
so shots were fired at the top of the stack to start its fall.
The following photos were taken of this event.
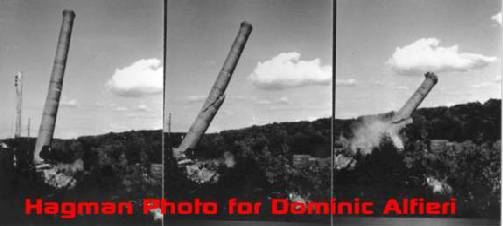
Two bricklayers, Tony
Pascarella and his son Monti, from
Clearfield
built a new one. They were later employed to do some other brick work.
A view of the factory viewed from the north side is shown here.
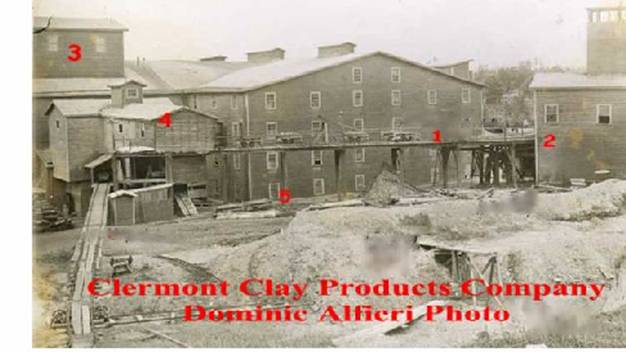
1.
Track that is used to take raw clay to a bin in a room above the dry pans 2.
Shaft house that houses the hoist from the mines (Charlie Nelson was the
hoist operator) 3. Room that has the screens
in it to screen the clay.4. Room where the clay bin is located directly above the dry pans in
which the raw clay is ground. 5. Track that
is used to take the coal to the boiler room.
Behind
the boiler room the Blacksmith Shop was located. The blacksmith in the early
days was Bill Reese. His duties included making and repairing various metal
things for the factory. In addition he shoed the mules that worked in the mines.
At
first the mules were housed in a barn near the factory but later a barn was
built for the mules on the former Frank Smith farm. They were kept in the barn
near the factory during the week while they were working and put out to pasture
at the other barn on weekends.
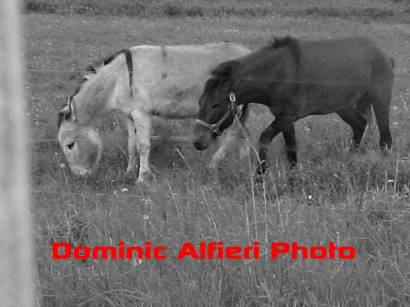
As you
face north, to the left of the factory were the kilns and their chimneys.
At first there were 12 kilns but in the early 1920’s Tony Pascarella
and his son Monti built 4 more for a total of 16.
There were 4 square smokestacks with each one serving 4 kilns.
There also was a small building that had gauges, which showed the
temperature of each kiln. This building also served as place for the kiln
firemen to eat their lunches or sit between firings of the kilns.
The kilns can be seen in the following photo.
This photo was taken at the time when construction of the additional
kilns can be seen.
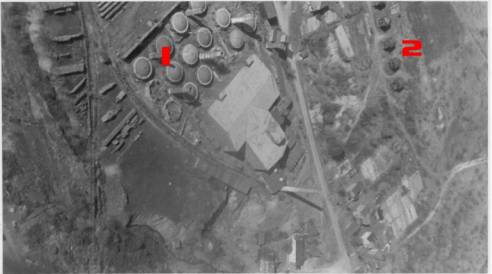
1.
View of kilns 2.
Black row of company houses
Each
kiln had 8 fireboxes around the outside where the coal was burned to heat the
kiln. It also had a large
round-topped door about 4 feet wide to enable the workmen to load it with the
material to be baked. These features can be seen in the photo shown here.
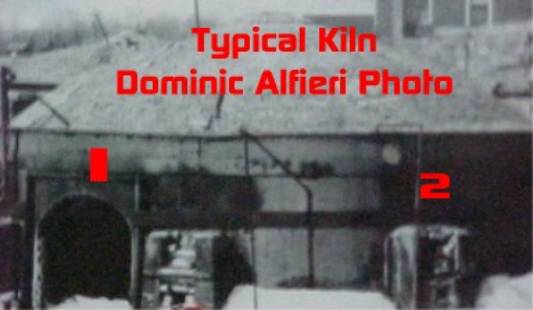
1.Door to Kiln 2. Firebox
After
the kiln was loaded the door was sealed with brick and soft wet clay with a
small tiny opening to permit viewing of the small heat indicators placed inside.
These indicators allowed the firemen to determine the degree of firing of the
tile.
There were 6 to 8 firemen employed to fire the kilns. The following were
employed in the early years. Frank
Miniaci, John Aloi, Tony Alfieri, Frank Butera, Natale Butera, Frank De Fazio,
and a man known as Felix. An accident happened one time when Felix had a seizure
and fell face down near a firebox and was burned very severally.
He carried horrible scars on his face after that. The foreman also worked
along with the men. He was also overlooked all the shifts. The foreman was Ralph
Aloi.
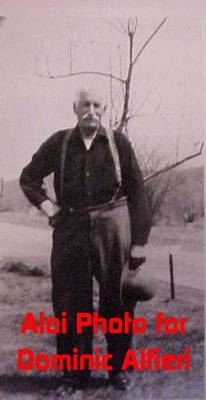
The four square chimneys that
served the kilns can be seen in this picture. It also shows some of the tile
yard where the finished tiles were stored until shipped by train to various
cities. At this time the factory had three presses for producing both large sewer
pipe and different size conduits. There were two vertical presses and one
horizontal press, which was called a plug mill.
One vertical press was located on the first floor and the other was on
the second floor. The clay was
brought from the mine in the shaft room and was delivered to a bin on the upper
track. There were two dry pans on
the first floor at the rear of the factory where the clay was ground into a fine
dust. It was hauled up to the screen
room on a bucket conveyor belt and screened. From the screens it went down into
a bin on the second floor.
The next process was mixing
water with the clay. The wet pans were located in the front right of the
building. A belt drove both the dry and wet pans from a shaft powered by the
engine from the engine room. A man called the clay temperor was responsible for
mixing water with the clay to the right consistency. The clay temperor was Punk
Johnson. After the clay had been mixed to the right degree of wetness and
hardness a bucket conveyer belt carried it to a slide above the press.
A man using a wooden paddle fed the clay into the press every time the
head of the press was raised. The
press crew consisted of the pressman, a former puller, and two men who placed
the green ware on a cart. Each cart was pushed by a man to the elevator in the
center of the plant and taken to one of the upper floors. Another crew of 2 men
would unload the tile on the floor for drying.
The smaller sewer pipes were placed directly on the floor while the large
ones were on a small wooden pallet.
For
all types of fittings there was a section of the second floor set aside as an
area where tees, wyes, ells, collars, reducers, elbows, and traps were molded.
These men had the title of molders.
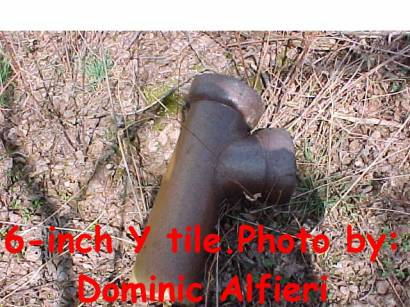
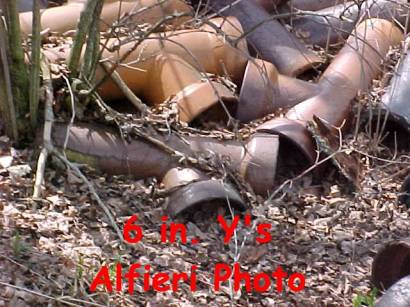
After the pipe were dry
another crew of men called the setting crew loaded the dry tile on carts and
took them down on elevators located on the rear of the building to the kiln
area.
Gerhart
Anderson was the boss of the setting crew. Some
of the members of the crew were Buster Amend,
Clyde
Reiner, and Fred Henry.
One
man in the plant had already cut rings from green pipe and these were used to
set the dry tiles on in the kiln. Usually
one man in the setting crew placed all the dried pipes in the kiln. After the
kiln had been completely full the door was sealed with brick and wet clay except
for a small hole the size of a brick in the door. A set of cones was placed on
the tile to be visible from this hole. Each cone was designed to melt at a
certain temperature and thus enabled the firemen to determine when the salt
glaze was to be applied and when the baking process was over.
After
the tile had finished baking and had been glazed, the brick and clay door was
removed from the kiln. The crew of men known as the “Draw Gang” loaded the
tiles on wheelbarrows and wheeled them on metal tracks to the tile yard. Members
of the gang were Carmen Grillo, Carl Brown, Clarence Silfies, and Clint Silfies.
Iroe Dibler served as inspector and used a small metal tool, which was used to
rattle the inside of each conduit to test for cracks.
They
were stored there until they were loaded in railroad cars to be shipped to
various cities.
Across from and west of the factory a house was built to serve as
an office.
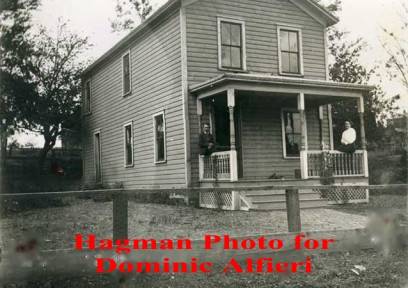
The
first superintendent was W.E. Ringrose, who with his wife Clara, lived across
the street on the same side as the factory.
Daisy Aloi who lived to the right of the company office spent a lot of
time at the Ringrose household. They became quite fond of her and even sent to a
school. Mr. Ringrose also provided
money for Tony Rizzo, son of Frank Rizzo, to go to college. Mr. Ringrose served
as superintendent until 1920. Jack Allison, a member of the Clermont baseball
team, was the shop foreman at this time. He was offered the job as
superintendent but instead chose to become Mc Kean County detective.
Consequently John Clay became superintendent and served until 1925. At this
point, with plenty of experience in this type of factory, H. K. Leighow took
over the operation. He remained at
the post until the plant closed in 1932.
The
manufacture of sewer pipe continued until 1919 when the company began to
manufacture tile conduits. During
this time all the major cities had all their telephone and electrical lines
suspended on poles. With the
expansion it became a major problem so the solution became fired clay tile
conduits. This way the lines could be put underground and the salt glazed
conduits would provide excellent cover. The
changeover was completed and production began. Western Electric Company became
their primary customer. It was necessary to produce various sizes from one-hole
conduits to one with nine holes. The larger tile had tiny holes in which iron
rods were installed to hold the conduits together. Here are some examples of
these conduits:
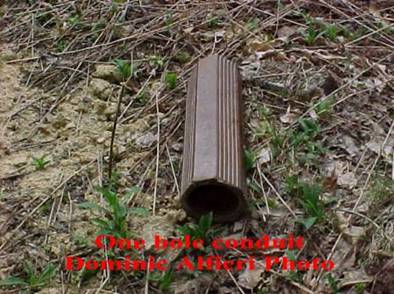
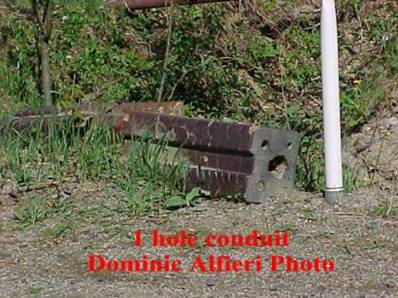
The small holes for the
iron rods can be seen in the center of the larger conduits.
These
conduits were shipped in boxcars by railroad to cities such as
New York
,
Philadelphia
, and
Boston
. To prevent breakage wooden frames called gates were made to separate the
conduits. A small house called the gatehouse in the yard was used as a place to
construct the gates.
Clermont
Clay Products Company Houses
As earlier
indicated before three rows of houses were built in 1904 when the plant was
built. They were called the Black
Row, King Row and Queen Row. Some of the tenants in the 1920’s, 1930’s and
1940’s were:
Black
Row:
Art
Marshall, Leander Marshall, Curt Marshall, Avery Brown, Carl Brown, Mike Valenti
and family, Everett Wells Family, Frank Butera, Christmas Butera, Steve Burfield
Family, Charlie Peterson Family, Glenn Snyder Family, and Albert Fuller family.
King
Row
Charlie
Nelson Family, Charlie Billings Family, Earl Eckerd Family, Bill Burford Family,
Jim Sample Family, Johnson Family, John Matthews Family, Harry Flickinger
Family, Art Marshall Family and Don Simonds Family
Queen
Row
Albert
Carter Family, Byron Nelson Family, Jack Sample family, Avery Brown Family,
Willard Rounsville Family, Fred Murray Family, Tony Spadafore, Fred Russell
Family, Ralph Salatino Family, Fred Russell Family, Jim Fowler and wife and
Smouse Family
As
indicated before Willard Rounsville managed the water works, which was owned by
the company but supplied water to other residents besides their company house.
The following bill made out to Jake Amend was given in the 1920’s.
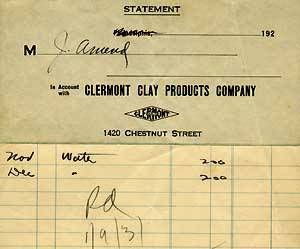
By 1930 the need for conduits
had waned in the cities since most of the lines had been laid.
With the slowdown in the economy and the eventual depression the plant
was forced to shut down in the early 1930’s.
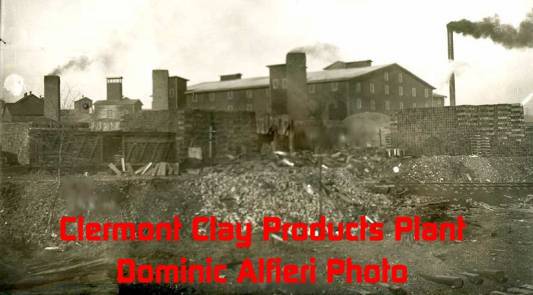